Disc Springs
Disc Springs are conically-shaped precision components designed to be axially loaded. Disc Springs are often incorrectly referred to as belleville disc springs, belleville springs, belleville washers or simply conical washers. Disc Springs are unique and differ from other types of springs in that the force/deflection curves of Disc Springs are consistent and repeatable, and the minimum fatigue life can be reliably determined (per the standardized calculations of DIN EN 16984 (formerly DIN 2092)). Disc Springs can be statically loaded either continuously or intermittently, or dynamically subjected to continuous load cycling. They can be used singly or in multiples stacked parallel, in series or in a combination thereof to achieve the desired force-deflection characteristic.
Disc Springs are preferred over other types of springs (such as coil springs, belleville washers, belleville springs and conical washers) when used in critical applications such as safety valves, clutch & brake mechanisms for elevators, and supports for industrial pipe systems due to their predictability, reliability and unparalleled fatigue life.
The advantages of Disc Springs compared to other types of springs include the following:
- A wide range of load/deflection characteristics
- High load capacity with small deflection
- Space savings – high load to size ratio
- Consistent performance under design loads
- Longer fatigue life
- Inherent dampening especially with parallel stacking
- Flexibility in stack arrangement to meet your application requirements
SPIROL offers the full range of DIN EN 16983 (formerly DIN 2093) Group 1 and 2 Disc Springs in Series A, B, and C. In addition to the DIN specified sizes, SPIROL stocks its own standard size range in outside diameters from 8mm to 200mm in order to meet the diverse needs of its customers. SPIROL standard Disc Springs meet all material, dimensional tolerance, and quality specifications as laid out in DIN EN 16983 (formerly DIN 2093) but in diameter and thickness combinations that are not included in the DIN standard.
SPIROL also offers a line of austenitic Stainless Steel Disc Springs.
SPIROL supplies single Disc Springs, as well as Pre-stacked Disc Springs in custom configurations, packaged in shrink wrap with a perforated tab for easy of assembly.
Select from our expansive standard offering, or take advantage of our complimentary Application Engineering support and allow us to work with you to help determine the most appropriate Disc Spring or Disc Spring Stack for your specific application and assembly needs!
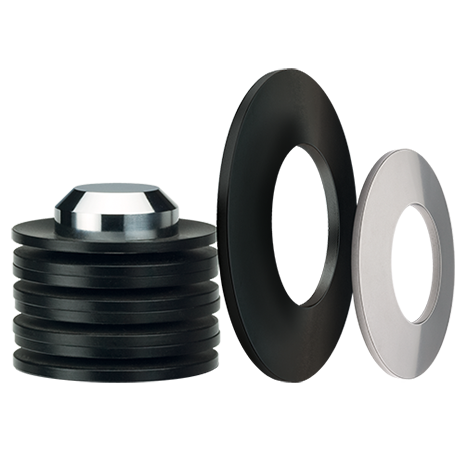
Disc Spring Types
SPIROL’s Disc Spring offering consists of 1) Disc Springs per DIN EN 16983 (formerly DIN 2093) , 2) SPIROL standard Disc Springs with outside diameters ranging from Ø8mm to Ø200mm designed around the standardized calculations of DIN EN 16984 (formerly DIN 2092), 3) Austenitic Stainless Steel Disc Springs and 4) Pre-Stacked Disc Springs.
Don’t See What You’re Looking For?
Need help choosing the right high-quality and effective fastening solution for your application? SPIROL’s expert engineers can design the most cost-effective Disc Spring solution for your application. Let us help!

Specifications
High carbon and alloy steel materials provide excellent strength and endurance life in most applications. The standard coating of zinc phosphate and oil provides adequate protection from humidity and occasional moisture. More effective protective finishes are available, but these tend to wear off in Dynamic applications.
Electroplated finishes should always be avoided. Hydrogen embrittlement poses too great of a risk in highly loaded Disc Springs having a hardness over HRC 40. Austenitic stainless steel is a very good choice for static and low cycle applications. It provides high forces and excellent corrosion resistance. This material will continue to work harden with use so cycle life is limited, but creep resistance is good.
For dynamic applications where corrosion protection is required, precipitation hardening stainless steels are recommended. These steels are nearly as strong as the standard Disc Spring materials and very corrosion resistant.
At temperatures over approximately 200°F (100°C), standard Disc materials can begin to creep, or take a set. Between 300°F – 400°F (150°C – 200°C) the materials lose their strength and are no longer considered viable. Stainless steels are a bit more temperature resistant, but only up to 575°F (300°C).
PROPERTY | GROUP 1 | GROUP 2 |
THICKNESS | <1.25mm | 1.25mm up to 6mm |
MATERIAL | B Carbon Steel C67S (1.1231) / UNS G10700 |
W Alloy Steel 51CrV4 (1.8159) / UNS G61500 |
HARDNESS | HV 425-510 (HRC 43-50) | HRC 42-52 (HV 412-544) |
FINISH | R Zinc Phosphate and Oil |
SERIES A | De / t ≈ 18 | ho / t ≈ 0.4 |
SERIES B | De / t ≈ 28 | ho / t ≈ 0.75 |
SERIES C | De / t ≈ 48 | ho / t ≈ 1.3 |
MATERIAL | D SAE 301 Stainless Steel Full Hard (X10CrNi18-8 No 1.4310 / UNS 30100) |
|
FINISH | K Plain finish, not oiled |
TO ORDER: Product Code / De / Di / t / Material / Finish
EXAMPLE: DSC 25 x 12.2 x 0.7 BR
Design Guidelines
SPIROL has outlined general design guidelines to help select the most appropriate Disc Spring or Disc Spring Stack configuration for your application. Factors to take into consideration when selecting the proper Disc Spring or stack of Disc Springs are forces, working parameters, environment, duty cycle, and required life. SPIROL offers design guidelines for:
- Sizing and Selection
- Fatigue Life
- Materials & Finishes
- Orientation
Access Disc Spring Design Guidelines
SPIROL provides complimentary Application Engineering support to not only help you select the most appropriate Disc Spring or Disc Spring Stack for your specific application, but to also help you design your assembly to achieve the desired performance for the life of the project. Feel free to contact us at any time to engage our Application Engineering Team!
Stacking
Stacking individual Disc Springs provides the designer with:
- A wide range of possible force/deflection combinations;
- The ability to design application specific load curves – both progressive and regressive; and
- The opportunity to design a range of dampening characteristics into the design.
Methods of Stacking
Consideration needs to be given to the friction between the parallel Disc surfaces. A reasonable allowance is 2–3% of the force for each sliding surface – a greater force for loading and a lesser force for unloading. Disc Springs in parallel should be well lubricated and it is suggested that the number of Discs in a parallel set be limited to a maximum of 4 to reduce the deviation from calculated to measured characteristics. Disc Springs in parallel have increased self-dampening (hysteresis) characteristics.
Stack Construction
It is normally desirable to have both ends rest on the larger outer edge of the Disc. With an uneven number of pairs in a stack, this is not possible. In this case, the end resting on the outer edge should be arranged to be on the end on which the force is applied – the moving end of the stack.
Application Success Stories

Disc Spring Stack in Mechanical Clutch in Heavy Duty Right Angle Drill
Customer Challenge:
The lead engineer at a prominent hand and power tool company contacted SPIROL for help determining the best Disc Spring design for a new lightweight, compact, and portable Heavy Duty Right Angle Drill.
SPIROL SOLUTION:
- SPIROL Engineering designed two special Disc Springs stacked in series to meet the specific force and deflection requirements.
- Disc Springs offer a higher load capacity in less space as compared to conventional coil springs which enables the designer to make the tool more compact.
- Unlike Belleville Washers that are mostly used in static applications, Disc Springs provide unparalleled predictability, reliability and fatigue life in highly dynamic applications.
- By partnering with SPIROL and incorporating our recommendation, the customer minimized costly development time and confidently launched their new high-quality drill to the market.
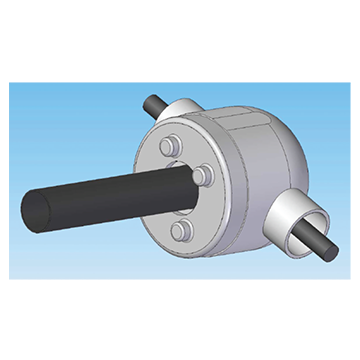
Disc Springs in Mechanical Braking System
Customer Challenge:
Braking systems for Off Highway equipment are commonly designed to be hydraulically actuated. In most cases, braking occurs when pressurized fluid compresses stationary plates against plates that rotate with the drive shaft. The amount of friction between each set of plates controls the deceleration of the vehicle. Without an additional fail safe system, this design alone has limited reliability. If a hydraulic seal is compromised, or the hydraulic cylinder loses pressure for any reason, the brakes fail.
SPIROL SOLUTION:
- The mechanical back-up design uses SPIROL® Disc Springs. Under normal circumstances, the hydraulic system holds a constant pressure on Disc Springs stacked in series. If pressure fails to be maintained, the stack of Disc Springs decompresses to actuate the braking mechanism. A compression spring or wave spring is not capable of providing the force required (in the space available) to actuate the brakes. The reliability of this safety system is dependent on the consistent performance of Disc Springs. In this critical application, the Disc Spring’s performance and level of predictability improves product quality and ensures overall safety.
- SPIROL® Disc Springs have a high capacity to consistently store releasable mechanical energy.
- The conical design of SPIROL® Disc Springs makes their spring characteristics and performance more predictable than traditional compression springs. Disc Springs are also capable of providing more force in less space than a compression spring or wave spring. They are commonly stacked in multiples to achieve application specific spring rates: a stack in series provides less force over more travel; a stack in parallel provides more force over less travel. The precise tolerances of each individual Disc Spring provides unparalleled performance predictability when they are stacked (either in series or in parallel).
- SPIROL® Disc Springs also allow fatigue endurance to be predicted. Stress analysis enables the minimum cycle life of Disc Springs (singularly or stacked) to be calculated as a part of the application’s design.
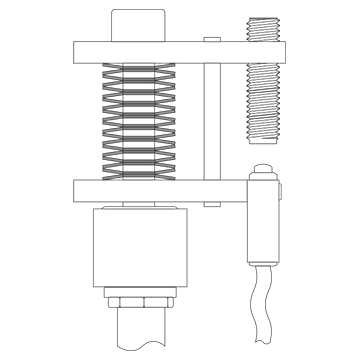
Disc Spring Stack in Crane Overload Safety Switch
Customer Challenge:
A manufacturer approached SPIROL for assistance on designing a stack of Disc Springs that would reliably activate an overload mechanism for a warehouse crane. The manufacturer’s design allowed the crane to function within a range 800 – 2400kg (7.85 – 23.54kN), and the Disc Springs were to activate the overload mechanism preventing the use of the crane at loads over 2700kg (26.48kN). The manufacturer’s design parameters limited the maximum Disc Spring diameter to 94mm and a stack height of 150mm.
Although the stop mechanism is only used on the rare occasion when the crane is overloaded, this is considered a dynamic application as the Disc Springs will be cycling each time the crane is used.
SPIROL SOLUTION:
- SPIROL’s Application Engineering Team determined that (20) alloy steel (51CrV4) Disc Springs (DSC 90 x 46 x 5mm WR) stacked in series would provide the nominal force/deflection requirements within the physical constraints of the design. To ensure the Disc Spring Stack would perform as desired at the minimum and maximum material conditions, SPIROL Engineering’s evaluation included calculating the performance of the Disc Spring Stack at the extreme limits of the tolerance range. This included the spring force tolerance of the Disc Spring (+10 / -5% @s = 0.75ho) coupled with ± 2-3% applied to the final force value to account for the minimal effect of friction between the Disc Springs since there were no Discs stacked in parallel.
- In the end, the recommended Disc Spring Stack met all performance requirements within the physical constraints of the design.
- For more information, read our White Paper “How to Determine the Proper Disc Spring Stack Configuration”
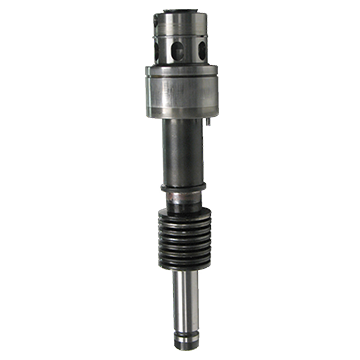
Disc Springs in Pick-Off Unit for CNC Machines
Customer Challenge:
Pick-off spindles in CNC screw machines are designed to hold a part as it is cut to length and then finished. The spindle uses a collet to release the part when it is complete and then clinch a new part.
SPIROL SOLUTION:
- When the machine is setup, the clamping force required to hold each part in the collet must be precisely calibrated to prevent the finished product from slipping (if the force is too low) or being crushed (if the force is too high). This calibration is dependent on the geometry and material of the final product. After calibration, the quality of the finished product relies on a consistent clamping force for thousands of cycles at a time.
- This high degree of reliability is provided by SPIROL® Disc Springs. When the collet is opened, 16 SPIROL® Disc Springs stacked in series are compressed by a hydraulic cylinder. Each time the force from the cylinder is released, SPIROL® Disc Springs provide a consistent force to close the collet on the part.
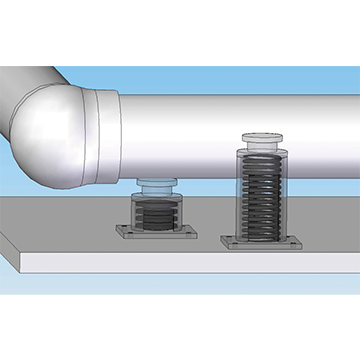
Disc Springs as Pipe Supports for Industrial Pipe Systems
Customer Challenge:
As mandated by the ASME code for pressure piping, proper design and installation is critical for the performance and safety of piping systems. Industrial pipe systems are primarily supported by rod hangers, base line or base elbow supports. While these static supports are used to carry weight, dynamic supports are necessary to control loads on the pipe system.
SPIROL SOLUTION:
SPIROL® Disc Springs offer an advantage to coil springs by providing an equivalent displacement in a fraction of the space. In many instances, such as under a heat exchangers bottom flange, this space savings is required. SPIROL® Disc Springs are the solution to providing a robust, maintenance free support system for industrial pipe systems.
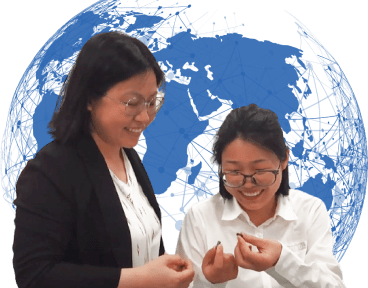
Local Design, Global Supply.
SPIROL has Application Engineers throughout the world to assist you in your designs, supported by state-of-the-art manufacturing centers and worldwide stocking facilities to simplify the logistics of delivering your product.
Have a manufacturing issue you can't solve? Our engineering experts love a challenge. Recommending efficient solutions for your application requirements is what we do best. Give us a call or fill out the form below to connect with us!
+86 021-5046 1451