Precision Metal & Custom Shims
SPIROL specializes in the custom manufacturing of tightly toleranced Precision Shims, Specialty Washers and Thin Spacers. Precision Shims are often used as compensators to absorb accumulated tolerances between mating components. Shims can also significantly reduce manufacturing time and costs as they eliminate the need for each component to be precision-machined to achieve the proper fit and function of the total assembly.
SPIROL manufactures Shims using a variety of stamping methods, machining processes and laser technology to meet your specific lead time and total cost considerations. Whether a project is for prototype, short run or long-term requirements, SPIROL has a solution to minimize costs by controlling – or even eliminating – tooling costs. In addition to having flexibility in our primary operations, SPIROL also performs most secondary processes in-house including heat treating, grinding, lapping, high speed polishing deburring, finishing and passivation. This enables SPIROL to maintain control over quality, cost and lead time for our Shims.
SPIROL produces Shims custom-made to customer specifications in thicknesses ranging from 0.02mm up to 25.4mm (.001″ up to 1.000″) from a comprehensive inventory of standard raw materials including, but not limited to:
- Carbon steel
- Stainless steel
- Aluminum
- Brass
- Copper
Our extensive inventory of standard raw materials, in both single sheet stock and laminated shim stock, enables us to provide quick turnaround delivery of your Shim production requirements. In addition to thousands of off-the-shelf standard material types and sizes, SPIROL will also manufacture Shims from any special material that we will procure from our certified raw material suppliers.
Different materials offer specific benefits depending on the application requirements including corrosion resistance, wear resistance and more. There are also a number of finish options available to protect Shims against particular environmental conditions such as exposure to salts and corrosives, humidity and galvanic corrosion. SPIROL’s Applications Engineers are here to support you in selecting the most cost-effective material and finish combination for your assembly!
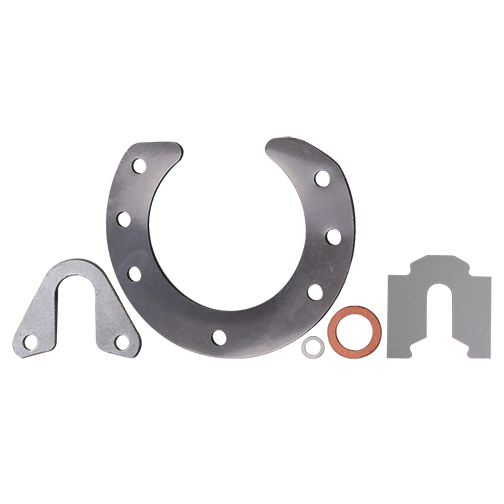
Shims Types
SPIROL manufactures a wide variety of different types of Precision Shims and sets the standard for product quality, service and value in the aerospace / defense, agriculture / heavy equipment, industrial equipment and other markets. In addition to Custom Shims, we specialize in Thin Spacers and Specialty Washers built specifically to your specifications. Our strength is cost-effective production of short run stampings in thicknesses ranging from 0.02mm (.001") up to 25.4mm (1.000") in quantities ranging from one piece to thousands. Here is a sampling of the different types of Shim products SPIROL offers:
- Flat Shims
- Thin Shims
- Heat Treated Shims
- Single Shims
- Adjustable Shims
- Laminated Shims
- Edge Bonded Shims
- Specialty Washers
- Thrust Washers
- Thin Spacers
Don’t See What You’re Looking For?
Need help designing a Shim for your application? SPIROL’s expert engineers are here to help!

SPIROL Shims at a Glance
SPIROL’s Precision Shim product line includes: Specialty Shims, Thrust Washers, Laminated and Edge-Bonded Shims in configurations ranging from simple OD/ID shapes to complex geometries. Products are custom-made to customer specifications from a comprehensive inventory of raw materials in thicknesses from 0.02mm (.001”) to 25.4mm (1.000”).
Manufacturing processes and value-added services are performed in-house under the direct influence of SPIROL’s quality system registered to ISO 9001, AS 9100 and IATF 16949 as well as the Nadcap accreditation for passivation and laser beam machining (LBM) and cutting. We can provide product — including prototypes — in quantities ranging from one piece to thousands. We also have qualified subcontractors for special requirements outside our capability.
Capabilities
Primary Operations
- Manual and automatic conventional stamping
- SWAT™ (Stamping Without a Tool) — a proprietary stamping process
- Large format fiber lasers
- State-of-the-art high speed machining centers
Secondary Operations
- Heat Treating
- Machining
- Grinding
- Lapping
- Micro polishing / deburring
- Edge bonding
- Part marking
- Specialty packaging
Tooling
- Standard tooling manufactured with CNC precision
Materials
- Global industry standard shim, sheet and coil stock, laminated materials and specialty metals in both inch and metric gauges
Finishes
- Passivation
- Black oxide
- Other finishes available upon request
- Zinc plate
- Anodized
- Cadmium plate
- Color coated
Custom Packaging Options
SPIROL packages our Precision Shims, Custom Washers and Thin Spacers to ensure dimensional stability and preserve microfinished and plated surfaces throughout the entire shipping process. This is especially important for very thin, delicate parts. Options such as Coin Wrap, Skin Pack or Vacuum Pack are available for such purposes. SPIROL offers other special packing options based on your unique requirements.
- Coin Wrap: Consists of stacking a number of round Shims and securely wrapping them in a rolled package similar to wrapping a stack of coins.
- Skin Pack / Vacuum Pack: Consists of placing a single Shim or multiple Shims on a cardboard backing, then affixing them through vacuum sealing.
Kit Packaging Options:
SPIROL offers different kitting options to simplify the assembly process and reduce total overall cost of the assembly.
- Shim Sets: Multiple thicknesses of a Shim are tied together. At the point of assembly, the operator would simply untie the Shim Set, separate the layers and install the Shim with the required thickness into the assembly.
- Edge Bonded Shims: Multiple thicknesses of a Shim are stacked and lightly bonded on the outer edges of the stack to provide an easy-to-separate Shim Set. This provides you with multiple thicknesses of a Shim without requiring multiple SKUs and inventory locations. Since the Shims are only lighted bonded together, the Shims are not damaged when they are separated from each other. Thus, the stack of peeled-off Shims can be put back into stock and used at a later date. This option enables you to specify the thicknesses, quantities of each Shim, and the order of assembly for the stack of Shims. Learn more about the advantages of using Edge Bonded Shims.
Application Success Stories
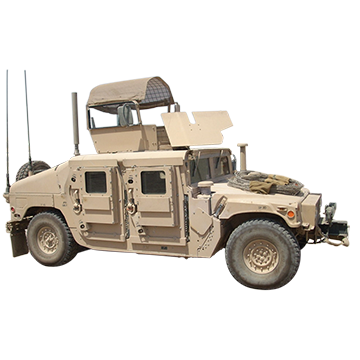
Shims in Armored Vehicle Door Hinges
Customer Challenge:
A military ground assault vehicle manufacturer approached SPIROL to provide quick delivery of adjustable Shim packs for spacing of armored vehicle door hinges. The spacing is critical to the welding process, providing proper sealing and locking engagement of the door systems. They considered using an adjustable Shim pack based on surface bonded Shim material requiring 94 layers of 0.002” thick laminates; however, given the size and configuration of the parts, surface bonded materials were very expensive, the manufacturing lead time was very long and the amount of time needed for dimensional adjustment exceeded their requirements.
SPIROL SOLUTION:
- SPIROL’s Application Engineering Team determined that an Edge Bonded Shim Set would provide the ground assault vehicle manufacturer with the best value and ease of assembly.
- Edge Bonded Shim Sets perform similarly to solid Shims, but rather than having to pick through various thicknesses of loose Shims and stack them in the proper position to achieve the required thickness, the thickness can be quickly selected from a single Shim Set and easily placed into the assembly.
- Edge Bonded Shims offer a number of advantages over Laminated Shims: The raw material is less expensive, the time to separate the laminations is much quicker, and the unused layers of Edge Bonded Shims can be used at a later time as they are not damaged during the adjustment process.
- Edge Bonded Shims are also safer to adjust as no knife is needed to remove the edge-bonded layers unlike the difficult-to-peel surface bonded layers of Laminated Shims.
- SPIROL’s Edge Bonded Shims offered safe, quick adjustment, a 70% cost reduction, and a short lead time. Furthermore, SPIROL’s solution eliminated the cost for tooling due to our expansive tool-less manufacturing technology.
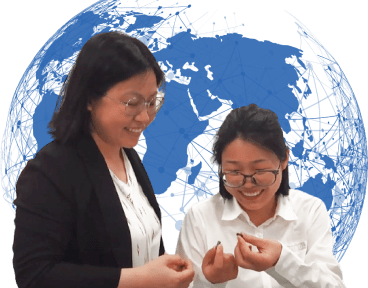
Local Design, Global Supply.
SPIROL has Application Engineers throughout the world to assist you in your designs, supported by state-of-the-art manufacturing centers and worldwide stocking facilities to simplify the logistics of delivering your product.
Have a manufacturing issue you can't solve? Our engineering experts love a challenge. Recommending efficient solutions for your application requirements is what we do best. Give us a call or fill out the form below to connect with us!
+86 021-5046 1451