DIN EN 16983 Disc Springs (formerly DIN 2093)
SPIROL offers the full range of DIN EN 16983 (formerly DIN 2093) Group 1 and 2 Disc Springs in Series A, B, and C. In addition to the DIN specified sizes, SPIROL stocks its own standard sizes with outside diameters ranging from Ø8mm to Ø200mm. SPIROL Standard Disc Springs were designed around the standardized calculations of DIN EN 16984 (formerly DIN 2092), and meet all material, dimensional tolerance, and quality specifications as laid out in DIN EN 16983 (formerly DIN 2093) yet offer an expansion in the diameter and thickness combinations that are not included in the DIN standard. Standard materials include carbon steel and alloy steel, both finished with a protective coating of zinc phosphate and oil.
In addition to single Disc Springs, SPIROL also supplies Pre-Stacked Disc Springs stacked in custom configurations, packaged in shrink wrap with a perforated tab for easy of assembly.
Application Engineering Assistance: If you would like assistance in selecting the proper Disc Spring Stack for your assembly, please Request Technical Support! We are here to help!
Shop Our Standard Disc Springs: For small quantities, click the Shop Now button below. For larger quantities or custom requests, please Request a Quote and one of our team members will get back to you quickly!
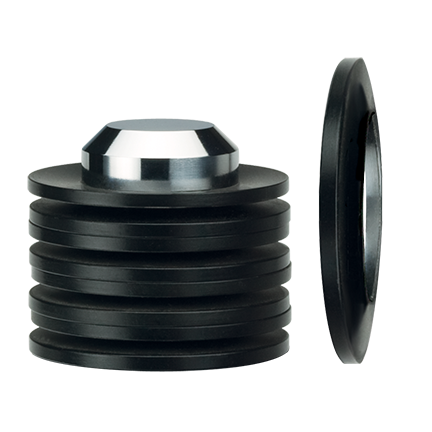
Disc Spring Product Offering
DIN EN 16983 (formerly DIN 2093) Range
SPIROL offers the full range of DIN EN 16983 (formerly DIN 2093) Group 1 and 2 Disc Springs in Series A, B, and C in outside diameters ranging from 8mm to 200mm.
SPIROL Standard Disc Spring Range
In addition to the DIN specified sizes, SPIROL stocks its own standard size range in order to meet the diverse needs of its customers. SPIROL Standard Disc Springs meet all material, dimensional tolerance, and quality specifications as dictated in DIN EN 16983 (formerly DIN 2093), however the diameter and thickness combinations are not included in the DIN standard.
Additional Disc Spring Options
Don't See What You're Looking For?
If you are unable to find the Disc Spring in the diameter, thickness, material, finish or quantity that you require with our standard offering, or if you are unsure which Disc Spring or Disc Spring Stack is most appropriate for your assembly, Request Engineering Support from our team and we will help you find the most cost-effective solution for your application.

Application Success Stories

Disc Spring Stack in Mechanical Clutch in Heavy Duty Right Angle Drill
Customer Challenge:
The lead engineer at a prominent hand and power tool company contacted SPIROL for help determining the best Disc Spring design for a new lightweight, compact, and portable Heavy Duty Right Angle Drill.
SPIROL SOLUTION:
- SPIROL Engineering designed two special Disc Springs stacked in series to meet the specific force and deflection requirements.
- Disc Springs offer a higher load capacity in less space as compared to conventional coil springs which enables the designer to make the tool more compact.
- Unlike Belleville Washers that are mostly used in static applications, Disc Springs provide unparalleled predictability, reliability and fatigue life in highly dynamic applications.
- By partnering with SPIROL and incorporating our recommendation, the customer minimized costly development time and confidently launched their new high-quality drill to the market.
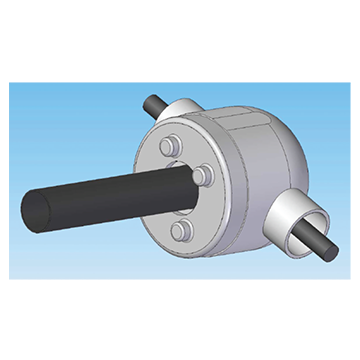
Disc Springs in Mechanical Braking System
Customer Challenge:
Braking systems for Off Highway equipment are commonly designed to be hydraulically actuated. In most cases, braking occurs when pressurized fluid compresses stationary plates against plates that rotate with the drive shaft. The amount of friction between each set of plates controls the deceleration of the vehicle. Without an additional fail safe system, this design alone has limited reliability. If a hydraulic seal is compromised, or the hydraulic cylinder loses pressure for any reason, the brakes fail.
SPIROL SOLUTION:
- The mechanical back-up design uses SPIROL® Disc Springs. Under normal circumstances, the hydraulic system holds a constant pressure on Disc Springs stacked in series. If pressure fails to be maintained, the stack of Disc Springs decompresses to actuate the braking mechanism. A compression spring or wave spring is not capable of providing the force required (in the space available) to actuate the brakes. The reliability of this safety system is dependent on the consistent performance of Disc Springs. In this critical application, the Disc Spring’s performance and level of predictability improves product quality and ensures overall safety.
- SPIROL® Disc Springs have a high capacity to consistently store releasable mechanical energy.
- The conical design of SPIROL® Disc Springs makes their spring characteristics and performance more predictable than traditional compression springs. Disc Springs are also capable of providing more force in less space than a compression spring or wave spring. They are commonly stacked in multiples to achieve application specific spring rates: a stack in series provides less force over more travel; a stack in parallel provides more force over less travel. The precise tolerances of each individual Disc Spring provides unparalleled performance predictability when they are stacked (either in series or in parallel).
- SPIROL® Disc Springs also allow fatigue endurance to be predicted. Stress analysis enables the minimum cycle life of Disc Springs (singularly or stacked) to be calculated as a part of the application’s design.
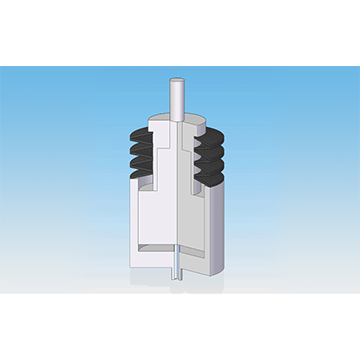
Turret Punch Press Assembly
Customer Challenge:
Traditional turret punch press tool designs utilize coil springs (die springs) to facilitate the stripping mechanism of a die. Rather than using a ram to push the punch through the sheet metal and pull it out, the spring automatically retracts the punch. This allows the ram to only have to work in one direction. The result reduces wear and extends the cycle life of the press.
SPIROL SOLUTION:
- Since the development of coil springs in turret tooling, engineers have been challenged to increase the productivity of turret presses even further. In a traditional press, the option of material type and material thickness is limited by the coil springs inability to produce a high force in a short linear distance. When this performance is necessary, coil springs will have a negative effect on the quality of the formed product and efficiency of the manufacturing process.
- SPIROL® Disc Springs are the solution to form thick materials, large extrusions, and more complex designs. When stacked in series (Figure 1), they are capable of providing a greater, more consistent stripping force than coil springs and require less space. They have become an instrumental component in the advancement of turret punch press tooling
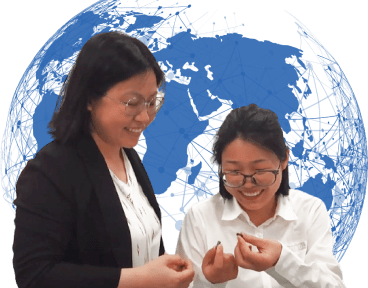
Local Design, Global Supply.
SPIROL has Application Engineers throughout the world to assist you in your designs, supported by state-of-the-art manufacturing centers and worldwide stocking facilities to simplify the logistics of delivering your product.
Have a manufacturing issue you can't solve? Our engineering experts love a challenge. Recommending efficient solutions for your application requirements is what we do best. Give us a call or fill out the form below to connect with us!
+86 021-5046 1451