How Pre-Assembled Disc Spring Stacks Help Manufacturers Save Time, Money and Ensure Quality
By
Download this WhitepaperOne of the most demanding and complicated components to construct in a production environment is the Disc Spring Stack. Disc Springs (sometimes referred to as Belleville springs / conical washers) are used in stacks to achieve very specific height, force and travel requirements within an assembly. Disc Spring Stacks can be constructed in a variety of formations including: in series, in parallel, and in both series and parallel.
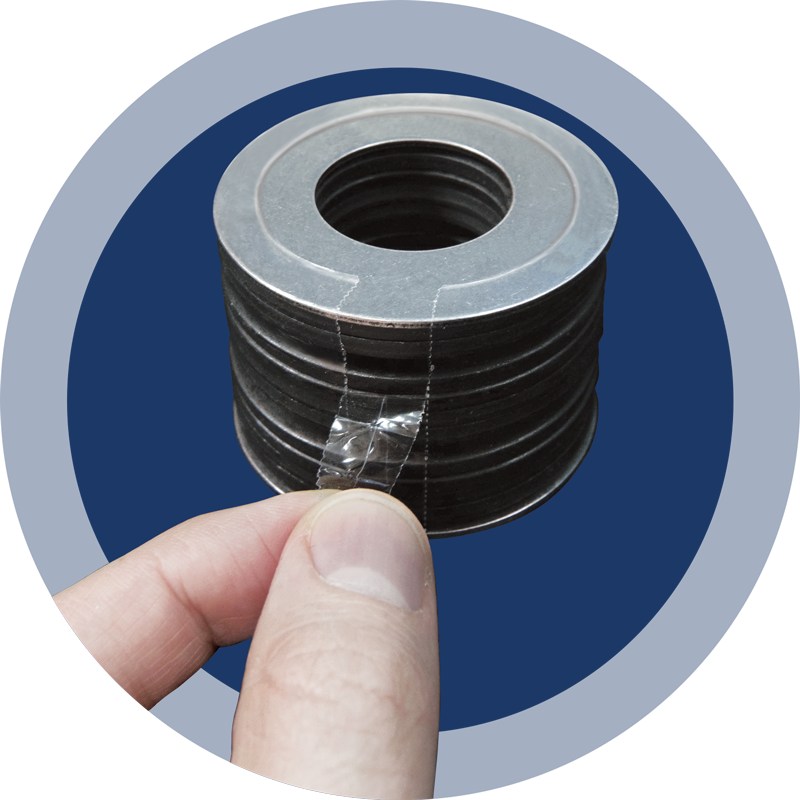
Figure 1 SPIROL Pre-Assembled Disc Spring Stack with easy-to-peel perforated tab
Methods of Stacking
In Parallel
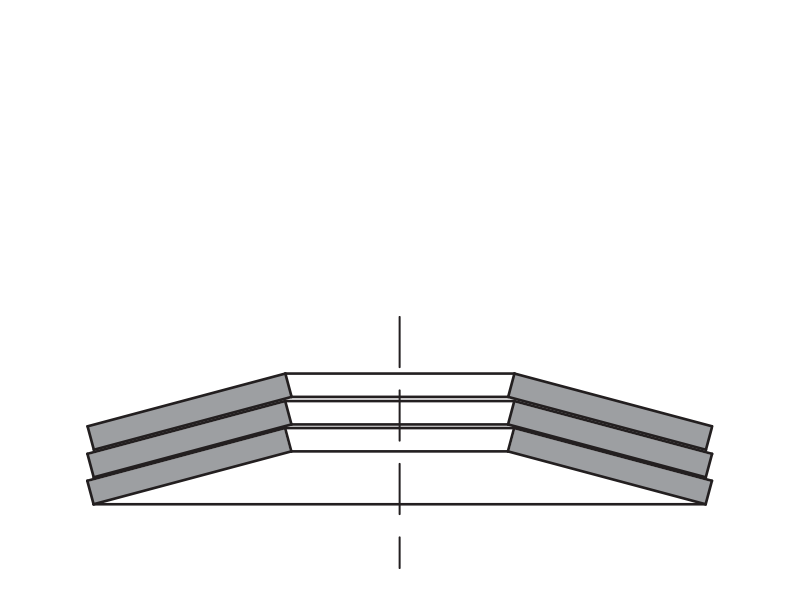
Deflection: Same as a single Disc Force: Single Disc multiplied by the number of Disc
In Series

Deflection: Single Disc multiplied by the number of Discs Force: Same as a single Disc
In Combination
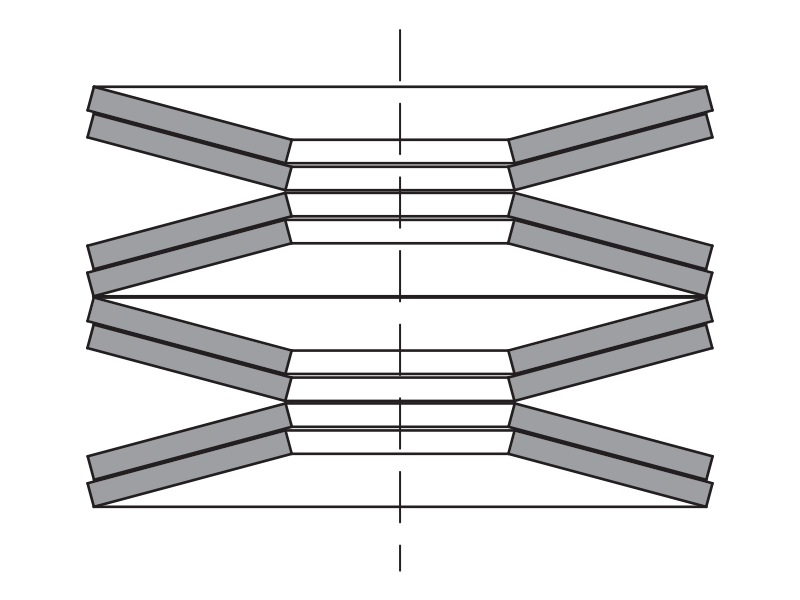
Deflection: Single Disc multiplied by the number of Discs in series Force: Single Disc mulitplied by the number of parallel Discs in a set
The Disc Spring’s outer diameter within the stack commonly ranges in size from 8 mm up to 200 mm. Some Disc Spring Stacks may contain Thrust Washers for stability (Figure 2). Disc Springs stacked in parallel are often lubricated to reduce friction between the surfaces of the individual Discs to curtail heat buildup that could otherwise be detrimental to the performance of the Disc Stack within the assembly. Given all of the variables that can go into the design of a Disc Spring Stack, there is no one universal rule on how to construct a stack.
When a Disc Spring Stack design is finalized and ready for production, the steps of creating the stack for the assembly begins. It is at this stage that important decisions need to be made:
- Where to source the Disc Springs / Belleville washers?
- What size Disc Springs are being used, what configuration do the Disc Springs need to be in, and how will this affect the production time needed to construct each stack?
- If the Disc Stack requires lubrication – what lubricant will be used and what is the best method to apply the lubricant consistently on each Disc Spring?
- Who will construct the Disc Stacks?
- How to train the assembler(s) to place each Disc Spring in its proper orientation every time?
- Does a jig need to be constructed to assist with the assembling of the Disc Stacks?
- How is quality checked on each Disc Spring Stack to ensure it is constructed correctly?
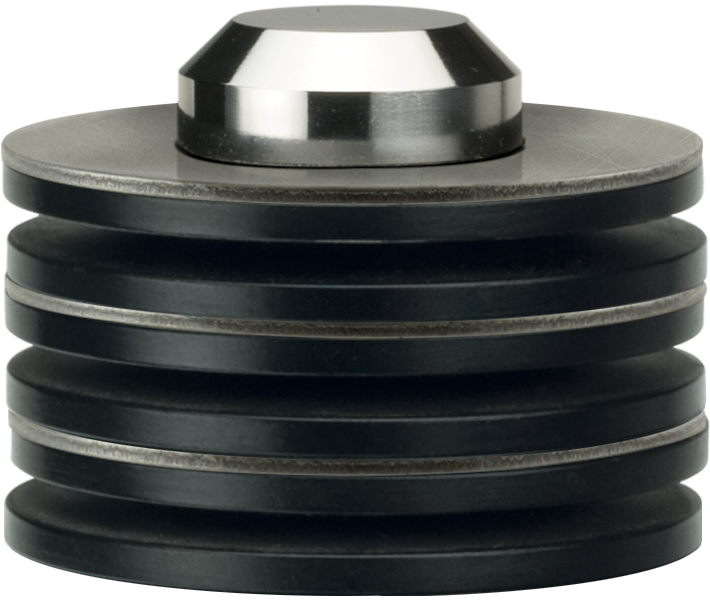
Figure 2 Disc Spring Stack with thrust washers
These questions need to be considered up front since some Disc Spring Stacks require technically skilled employees to construct the stack while others are more straightforward. If one Disc Spring in a stack is missing or is placed in an incorrect orientation, the performance of the Disc Spring Stack, as well as the life cycle of the product in which it is used, will be impacted. The same holds true with lubricants used between each Disc Spring stacked in parallel. Too much or too little lubrication may have a drastic effect on friction. Any of these missteps could shorten the life of the Disc Spring Stack and have a catastrophic impact on the assembly in which it is used.
An alternative to purchasing single Disc Springs and stacking them in-house is for manufacturers to purchase Pre-Assembled Disc Spring Stacks (Figure 1). Purchasing from a Disc Spring manufacturer that utilizes automation for sorting, lubricating, assembling, packaging, inspecting and shipping Pre-Assembled Disc Springs Stacks is an additional advantage.
Benefits to Purchasing Pre-Assembled Disc Spring Stacks Include:
- The time required to construct the Disc Stack is eliminated.
- Consistent lubrication between the Disc Springs is achieved – with no mess.
- The need for extensive training on how to properly assemble the Disc Spring Stack is eliminated.
- The requirement to design and build an assembly jig is eliminated.
- Quality and mistake-proofing of each stack configuration is eliminated.
- The time to complete the assembly process is significantly reduced, as each Disc Spring Stack is now simply a single drop-in-place unit.
The Purchasing process is also simplified as the Disc Spring Stacks are ordered as a single (completed) unit rather than each Disc Spring being ordered individually. Customized packaging enables trouble-free shipping of the Disc Spring Stacks without worry of the stacks disassembling during the shipping process. As needed, the Disc Spring Stacks can simply be pulled from inventory as a completed unit and delivered to either the production floor or to field operations. In addition to providing trouble-free shipping and storage, the robust packaging is equipped with features to facilitate easy removal once the Disc Spring Stack is positioned in the assembly.
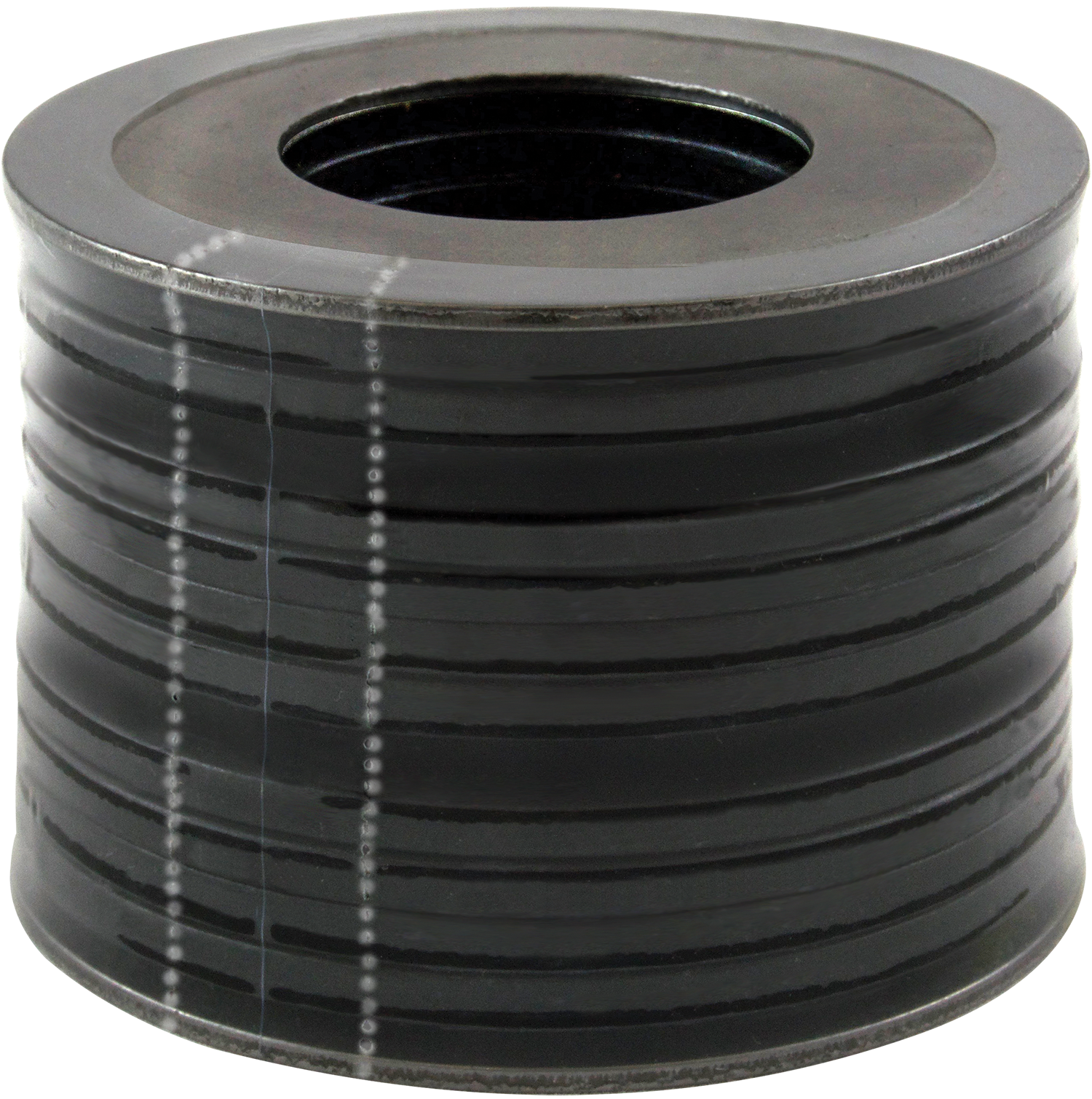
Figure 3 Pre-Assembled Disc Spring Stack
Conclusion
When manufacturers use Pre-Assembled Disc Spring Stacks (Figure 3) rather than purchasing single Disc Springs and stacking them in-house, they are easily able to save time and money while ensuring the quality of their final assembly.